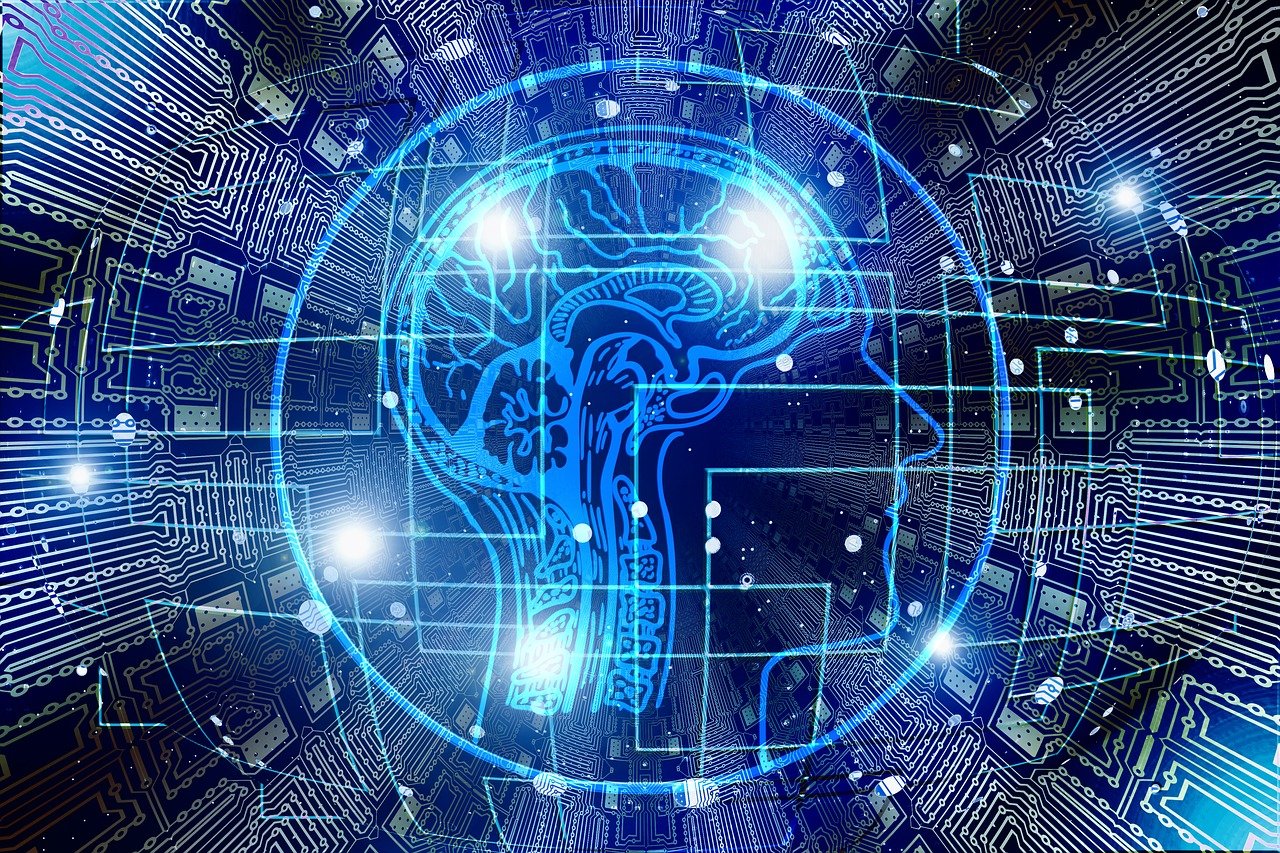
The connectivity of production processes has been the trigger for the transformation that the industry has undergone in the months after the pandemic.
Production and distribution chains have been favored by being able to link production processes and thus improve the way in which goods are mobilized, stored and distributed.
The Distribution Centers or CEDIS have benefited the most from this technological advance by allowing them to develop a competitive advantage for their organizations that not only impact production but also influence the new skills and abilities that those who operate them must possess.
Coordinating the physical flow with the flow of information demands hyperconnected systems through the cloud that generate a large amount of data and information that we must be able to manage.
The new way of doing things has led the CEDIS to demand the transformation of
smarter and more adaptable automation processes. The new smart warehouse must be able to integrate and manage technologies in its processes, getting the maximum performance and productivity from them. Let's look at some of these advances:
ERP with integrated WMS, the first one is in charge of the integral management of the logistics organization and the second one will take the warehouse organization more specifically.
The collaboration of both systems opens the doors to technological innovation and logistics 4.0 since they allow the coordination of practically the entire logistics chain thanks to the use of the Internet, electronic data exchange, Big Data processing or connection to the cloud.
Radio frequency terminals and 3G and 4G devices, smart devices that allow data to be captured while sending and receiving information in real time inside and outside the warehouse.
Thus, the operator can connect to the data of the WMS system that he requires to carry out his activities, at the same time that he knows all the actions of each operator with exact data, in real time and without restricting his movements.
Technology and picking. The order preparation activity is decisive in operating costs as it involves travel, handling, packaging, preparation, consolidation and palletizing, among other activities.
The possibilities range from Pick to light, Putt or light, Pick by voice and visual Picking with augmented reality.
The first one is the most intuitive where the guidance system is very simple. Displays with buttons are installed on the front of the picking rack that light up indicating the position from which it must be extracted and the exact quantity to be taken.
The second adds the possibility of guiding the operator to deposit the reference extracted in the picking. Third replaces lights and displays with voice.
Check here: Automotive sector dominates investments in Nuevo León
Artificial vision systems that support quality controls, also allow the detection of packaging, product or identification failures, making sure that each reference is in the proper position, perfectly identified and with legible identification.
This reduces the time of repetitive control processes in the warehouse, and minimizes product returns due to packaging or marking failures.
Automation and robotics in the warehouse, either through industrial robots or collaborative robots. While the industrial robot has been thought, designed and programmed to work on a single task that it performs perfectly, the collaborative robot works at the service of the operator by collaborating with him, it is easy to reprogram and, since it can perform several tasks, it is more versatile.
Stacker cranes and Pallet Shuttle systems, automatic storage systems capable of handling pallets or boxes and placing them on their racks and the Shuttle system works on compact racks bringing or placing the load that is requested or deposited on them.
Conveyors and electrified monorails, both are cargo transport systems, the former are anchored to the warehouse floor and the latter are not. Normally, conveyors are closely associated with stacker cranes, but like electrified monorails they can be used without the presence of these to save travel with traditional equipment.
Self-guided vehicles move autonomously along a guided path and are equipped with forks similar to those of forklifts.
Systems for sealing, shrinking and wrapping boxes and pallets, with infinite possibilities, from fixed to mobile, from simple turntables to robotic arms and machines that calculate the amount of filling required for each load.
Of interest: Coppel starts operations with a new CEDIS in Monterrey
Exoskeletons are conceived as personal protective equipment or PPE to help the worker by providing greater ergonomics, to perform heavy tasks or with postural risk, distributing the load in different parts of the body and in some cases providing additional mechanical help.
Adaptability is the key to the future and new technologies open the way for us to carry out automation projects in CEDIS. These innovations hardly alter the warehouse structure.
At the end of the day, it is about optimizing production processes reaching high levels of efficiency at affordable costs thanks to technology, working with Big Data in the cloud, making our systems collaborate with each other, performing electronic data exchanges in real time at Through the Internet, we are facing a new technological transformation.
Stay up to date with the most important news to the real estate
Subscribe Solili Newsletter